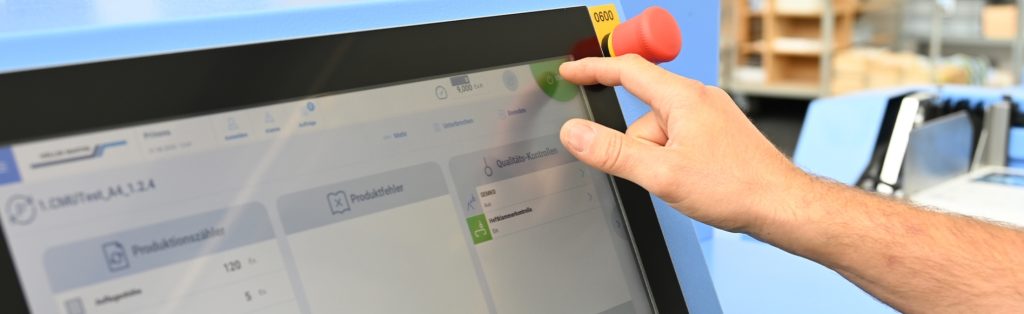
Legacy bindery equipment requires machine operators with deep mechanical and bookbinding knowledge. These must be combined with job-specific information to achieve high production speeds in the first place. Employees with these skills are hard to find in today’s job market and it takes a long time to acquire this experience.
With the latest user interfaces and a non-contact barcode workflow, Muller Martini simplifies machine operation. Manual contact points at the machine are minimized and repetitive setups are automated. Our setup wizard, combined with 2D barcode technology, are key features that reduce operator skill requirements. This allows you to choose from a much larger pool of labor for your bindery.
Sophisticated user interface
For over 25 years, Muller Martini has been developing machines with so-called Programmable Logic Controllers (PLCs) interfaces to facilitate machine operation and job changes. Once a novelty in the bookbinding industry, PLC user interfaces are now a core differentiator for profitable operation. The Muller Martini Setup Wizard is integrated into all our control systems, fusing our decades of knowledge and experience into a simple and sophisticated user interface.
Standardized operation
A powerful response to the challenges of today’s job market, the setup wizard provides novice machine operators with a standardized and repeatable sequence of steps that simplify changeover and machine operation and enforces best practices. This means that prospective machine operators need less knowledge and the training required for new employees is reduced.
But even experienced operators will appreciate being able to create setup templates to automate changeovers for repeat jobs and common size formats. The basic structures and operating philosophy are identical for all new Muller Martini machines, which also makes it very easy to switch operators from one machine to another.
2D barcodes
As a founding member of the CIP4 consortium, Muller Martini played a central role in the development of the JDF standard used across the industry as a common language for job definition and data transfer among devices in the print shop. We have extended this technology with the use of 2D barcodes, which gives you the following advantages:
- Automate machine setup, product integrity, and linkage across processes and machines.
- Encrypt your job information upfront for each job – varying trim sizes, production runs or personalized content – and the machine takes care of the rest. This minimizes costly and time-consuming human intervention and errors.
- Interfaces to other systems, databases, servers and even an Internet connection are no longer required. All the information needed for order processing is printed in a barcode on each book to automate all downstream processes.
Case study with barcode protocol
Linemark Inc., a commercial book manufacturer in Upper Marlboro, USA, recently invested in new finishing equipment from Muller Martini to increase efficiency in the production of its photo books, yearbooks and commercial hardcover and softcover books. Together, we collaborated to develop a customized barcode protocol to automate several manual tasks:
- Assure correct match of covers to book blocks in the Vareo PRO perfect binder.
- Provide book-specific information for inline trimming of books of any size in the InfiniTrim three-knife trimmer.
- Scan and reprint barcode information on blank endsheets
- Recall common size templates for the new EMP casing in machine.
So if you are thinking about reducing the manual steps in your company, contact your Muller Martini contact person. You can discuss with him or her how the contactless barcode workflow can improve the profit and productivity of your operation.
Yours,
Randy Shannon
Sales Muller Martini Region North America
This text is reproduced with kind permission of Müller Martini, you can read the original article first published here.